What is a Chilled Beam?
A chilled beam is a type of convection HVAC system designed to heat and cool spaces, typically deployed in open plan office buildings. Tubes are passed through a 'beam' (a heat exchanger), either directly integrated into a suspended ceiling, or hanging below the suspended ceiling of a room.
There are two types of chilled beams in use today:
- A passive beam chills the air around it, forming a natural convection current where cooled air falls and warmer air rises to replace it, therefore cooling the space.
- Active chilled beams are widely used as well, and use air from an AHU to induce additional airflow over the beam.
The principal challenge with this application is the control of the water temperature and flow rate, assuring that the surface temperature of the beam doesn’t fall below the dew point of the space.
Schematic
The figure shows the schematic of a chilled beam application using an Energy Valve. This provides the following control functionality:
- Accurate measurement of volumetric fl ow and the supply and return temperature
- Monitoring and control of thermal power of the unit
- Permanent hydronic balancing of the water fl ow at changing system pressures and in any load condition
- Optional integration of a dew point sensor switch
- Required delta T on chilled beams is very low, making managing them, critical
Common Issues in Chilled Beam Applications and Why You Should Choose the Belimo Energy Valve™
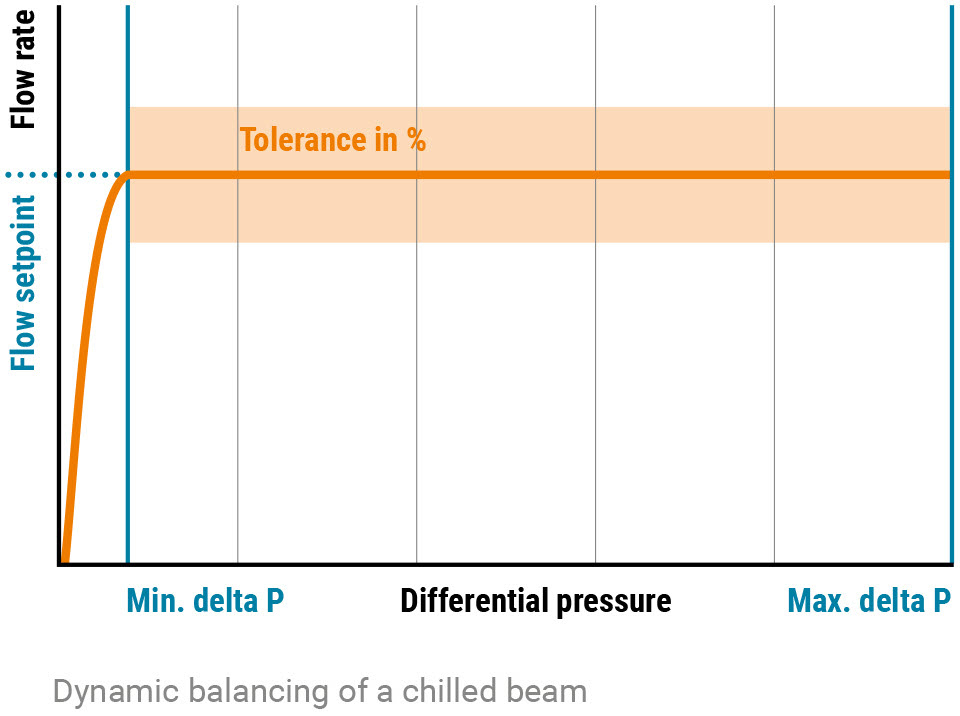
Low water temperatures and insufficient humidity control can lead to condensate forming on the chilled beam, and can subsequently damage furniture of office equipment that can be costly. However, conservative supply water temperatures can result in insufficient cooling capacity.
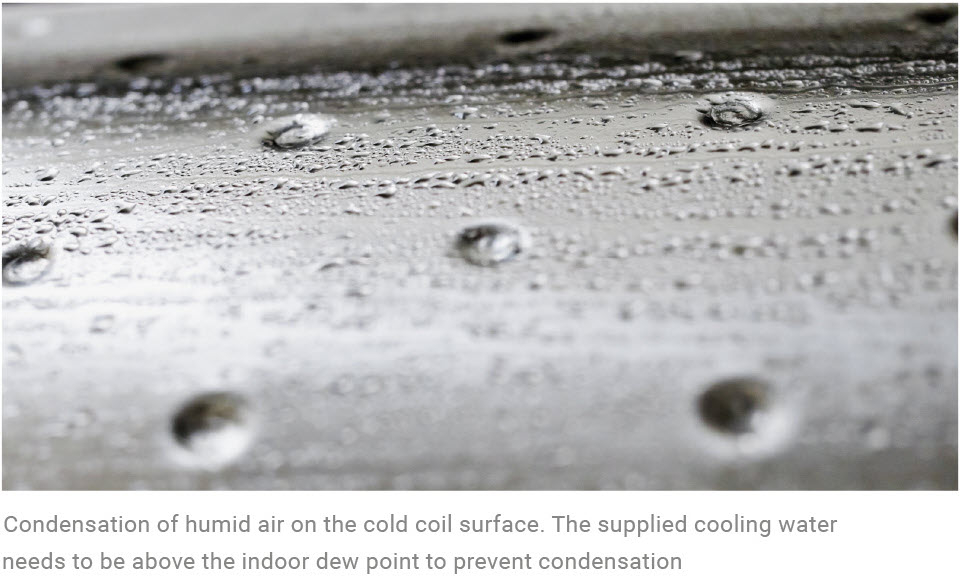
Using the more accurate and responsive immersion flow sensor from the Belimo Energy Valve™, DDC systems are able to detect and close-off water flows before condensate forms on the chilled beams. Reliable data from both the space and the water temperatures is the key to maximising chilled beam performance, while minimising the risk of condensate forming. An outdoor humidity/temperature sensor, such as the Belimo 22UTH-11, can be used to measure the outdoor air conditions and to adapt the AHU-control accordingly.
Supply air into the occupied space, and the circulated air from the room, pass over the coils of the chilled beam. The indoor dew point must be maintained below the surface temperature of the chilled beam coil to prevent condensation water dropping from the ceiling.
The primary air system in the AHU is used to offset the space latent load, and it typically maintains the indoor dew point at or below 13 °C [55 °F] to prevent condensation. Also, the water temperature delivered to the beams is typically maintained between 14 °C [58 °F] and 16 °C [60 °F], sufficiently above the dew point of the space.
Pro Tip
Consult local standards on recommended room air temperatures and humidity values (or maximum values), as well as recommended cooling water temperatures If you have smaller cooling loads in the room or large cooling surfaces, the cooling water temperatures can be raised by a few degrees (for example, up to 18 °C). It should still be possible to maintain sufficient cooling in the room, and thus dehumidification can be carried out in an energy saving way.
Application Example
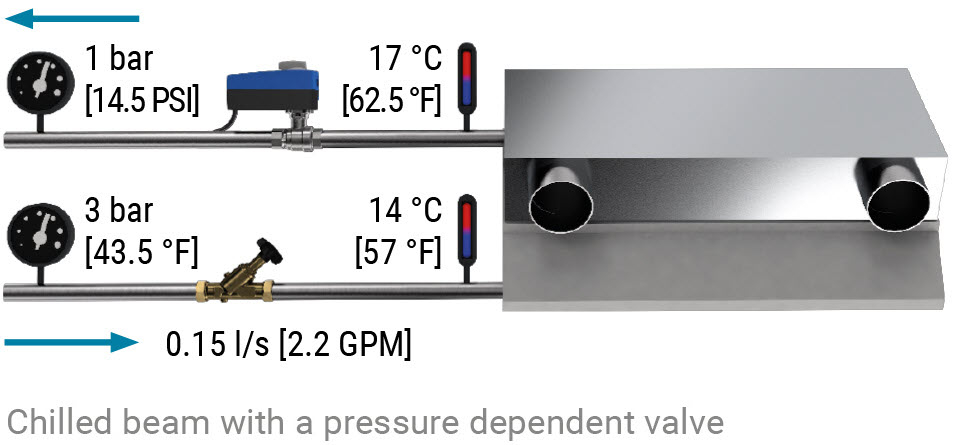
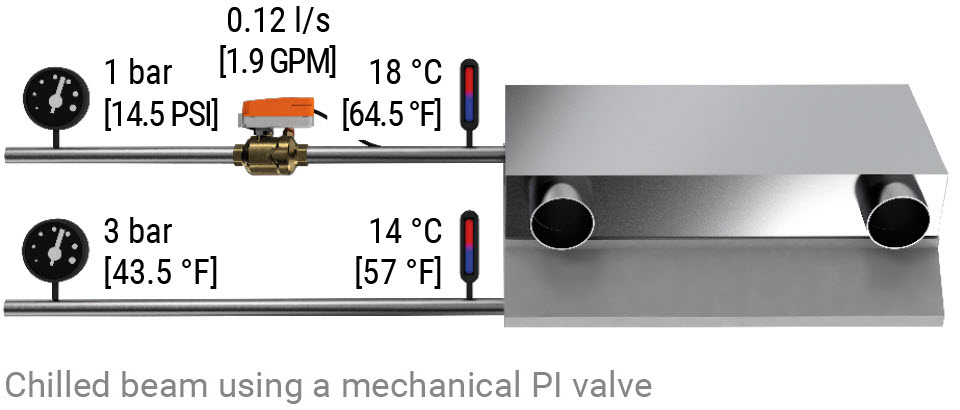
The Energy Valve will keep the flow as designed regardless of pressure fluctuations, at 0.12 l/s [1.9 GPM]. It will also manage the delta T over the coil and provide all essential data regarding flow, temperatures and energy to the BMS. Using the data available from the EV, many other value-added features are available, such as early detection of likely condensate issues.
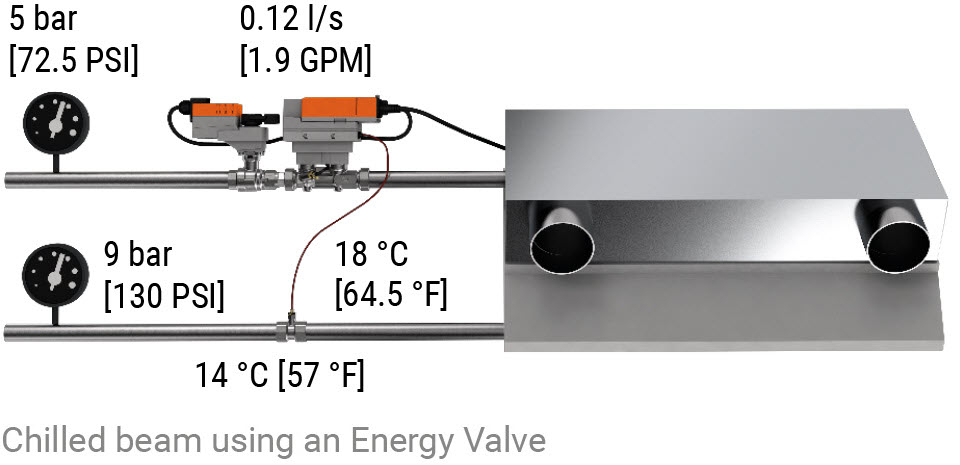
As shown below, the Energy Valve is on the same network as the sensor and the BMS head-end PC. The BMS is looking at the water flow temperature and calculating the dew point, using the RH and temperature data from the room unit. The BMS has seen the entering water temperature is at dew point, and has commanded the valve to close, in order to prevent condensate forming on the unit. The Delta T manager will keep your beams optimized when air flows over the coil vary.
